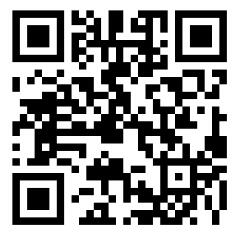
旋轉(zhuǎn)窯擋輪液壓缸的工作特點是運行速度低,活塞桿有偏心負(fù)荷,旋轉(zhuǎn)窯輻射溫度高,污染大,運行環(huán)境差。液壓缸為單作用缸,活塞桿的伸出由液壓力驅(qū)動,依靠旋轉(zhuǎn)窯的下滑力回程。液壓缸缸徑360mm,活塞桿徑110mm,工作行程120mm,額定工作壓力6.3MPa。圖2-4活塞與缸筒內(nèi)表面采用Yx形圈或O形圈密封;活塞桿與缸蓋之間采用銅套作為導(dǎo)向套,采用Yx形圈密封;Yx形圈或O形圈的材料為聚氨酯或丁腈橡膠;為了減少活塞桿在導(dǎo)向套上的徑向力,在導(dǎo)向套上安裝了兩個導(dǎo)向在導(dǎo)套上安裝液壓缸運動,減少活塞桿上的徑向力。實踐表明,這種結(jié)構(gòu)型式的擋板液壓缸使用效果不好。存在的問題是導(dǎo)套磨損嚴(yán)重,密封故障,內(nèi)部泄漏大,液壓缸端蓋有外部泄漏,液壓缸無法排氣或爬行。據(jù)統(tǒng)計,擋輪液壓缸壽命短的只有幾天,長的也不超過3個月。經(jīng)常維護(hù)不便,造成人力和物力大量浪費,嚴(yán)重影響了擋車液壓缸的壽命和性能。
導(dǎo)致?lián)踺喴簤焊资褂脡勖偷脑蚩偨Y(jié)如下5種情況。
1)徑向力過大,導(dǎo)向套磨損嚴(yán)重
如果圖2-4中的導(dǎo)向套安裝誤差小,工作狀況良好,可以保證活塞徑向力小,避免導(dǎo)向套過快和過度磨損,實際上擋輪裝置及其導(dǎo)向套的組裝是人的經(jīng)驗完成的,導(dǎo)向套長,安裝精度難以保證因此,擋板裝置的導(dǎo)向桿不能正確導(dǎo)向,擋板在活塞桿上的徑向力過大。過大的徑向力使活塞桿與導(dǎo)套的接觸面無法形成油膜,導(dǎo)套磨損嚴(yán)重。圖2-4顯示,液壓缸中的無桿缸沒有油壓,Yx圈的嘴唇不能張開,緊貼在配合的端蓋內(nèi)孔上,不能形成可靠的密封,因此發(fā)生了泄漏。同時,環(huán)境輻射溫度高、外部污染等因素使內(nèi)部泄漏和外部泄漏更加嚴(yán)重。
2)密封件選擇不當(dāng)
密封件的選擇應(yīng)根據(jù)液壓缸的使用環(huán)境、負(fù)荷狀況、工作壓力、工作速度的大小和變化狀況等具體要求,正確選擇符合其的密封件結(jié)構(gòu)形式。目前,國內(nèi)制造商使用的擋板液壓缸選擇Yx形環(huán)或O形環(huán)。由于擋輪液壓缸的輸入流量小(不超過15mL/min),運行速度低(不超過0.3~0.5mm/min),所以選擇的密封件內(nèi)的泄漏極小, 不要泄漏,而YX圈或O圈的泄漏量大,其結(jié)構(gòu)形式不能滿足使用要求。另外,擋板液壓缸選擇的Yx形環(huán)或O形環(huán)材料為聚氨酯或丁腈橡膠,其使用溫度一般在80℃以下,擋板液壓缸所在環(huán)境的輻射溫度接近70℃,在這個溫度下,Yx形環(huán)或O形環(huán)必然會發(fā)生一定程度的&ldquo軟化&rdquo不耐磨,容易蠕變,密封處的實際預(yù)壓力比設(shè)計預(yù)壓力小,液壓缸的內(nèi)泄漏量更大。當(dāng)活塞桿存在偏心負(fù)荷和彎矩作用時,活塞中心線必然與缸筒中心線相對偏移,一側(cè)間隙變小,另一側(cè)間隙變大。間隙變小的一側(cè),活塞和缸筒之間磨損嚴(yán)重,有可能發(fā)生氣缸拉動現(xiàn)象的間隙變大的一側(cè),密封圈被擠入間隙,密封圈被切斷,密封圈被破壞,密封圈的壽命縮短。
4)活塞上沒有設(shè)置限位裝置
目前,上下運行的極限位置在限位開關(guān)和導(dǎo)向棒的兩端加入擋鐵限位。但是,在實際運行中,由于液壓站停止,限位開關(guān)無法發(fā)揮作用,或者由于安裝不當(dāng),導(dǎo)向棒的下端擋鐵厚度不足,筒體的下端位置由某個擋車缸限制。在這種情況下,液壓缸中的活塞與缸底接觸,缸底直接承受回
轉(zhuǎn)窯的下降力。由于存在較大的導(dǎo)向誤差,在旋轉(zhuǎn)窯的下滑力和周期沖擊力的作用下,活塞有一定程度的偏移,在外力的作用下,活塞兩端面對應(yīng)的外圓部分嵌入缸筒的內(nèi)表面,出現(xiàn)半圓弧的槽,缸筒損壞,難以修復(fù)。
5)擋輪液壓缸沒有設(shè)置排氣裝置
液壓缸的進(jìn)氣口設(shè)置在缸底的中心,因為液壓缸的上部沒有設(shè)置排氣裝置,所以液壓缸的空氣不能排出,液壓缸爬行。另外,在液壓缸中保持壓力,管接頭松動或拆卸管接頭時,大量高壓空氣夾雜油液噴出,引起安全上的危險。
。